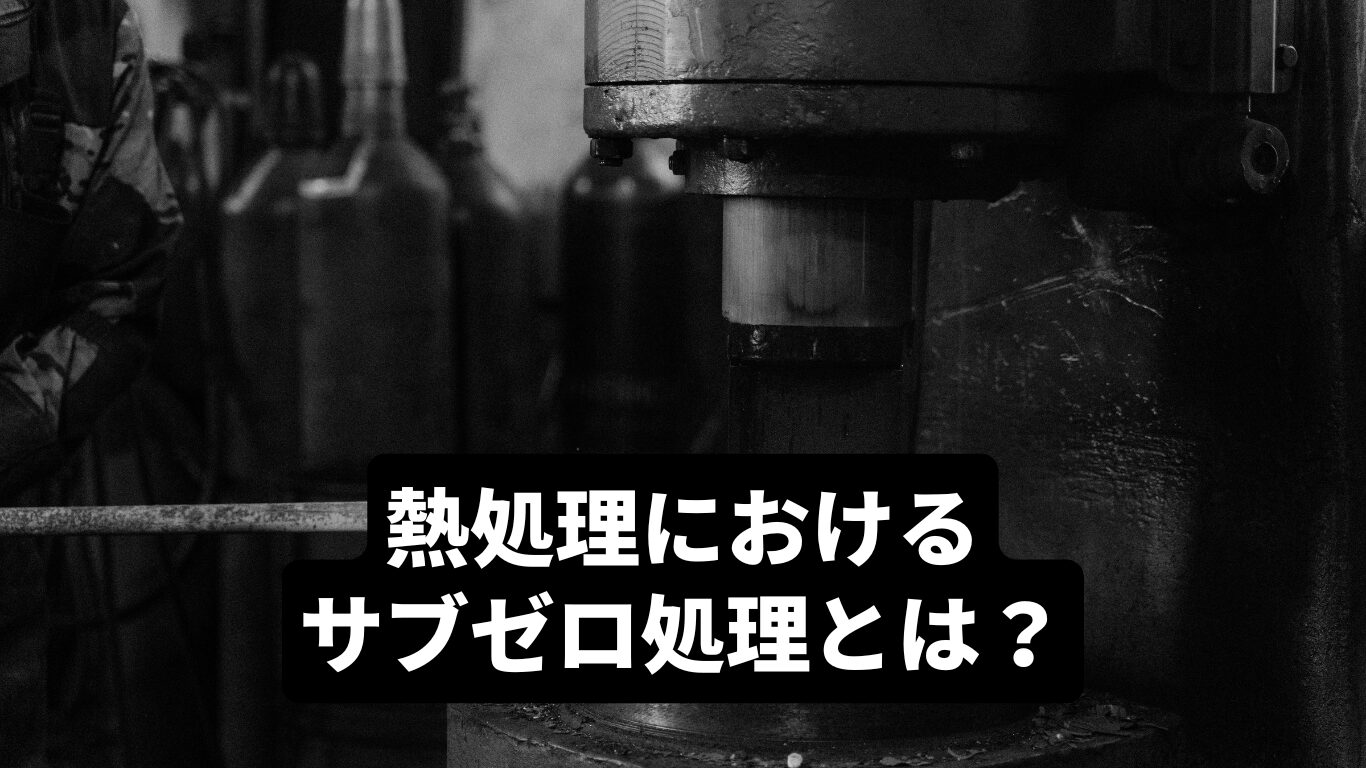
熱処理の専門知識をもっと深めたい方へ!今すぐ株式会社ウエストヒルの会社案内資料をダウンロードし、最新の技術情報と実績をご確認ください。
→ ウエストヒルの会社案内資料を無料ダウンロード
はじめに
高硬度・高精度が求められる金属製品に対し、焼入れ処理だけでは十分な性能が得られないことがあります。とくに寸法安定性や残留応力に課題を抱える部品では、時間の経過とともに変形や硬度低下が生じるケースも少なくありません。こうした問題に対処するために用いられるのが「サブゼロ処理」です。非常に低い温度で処理を行うこの技術は、残留オーステナイトの除去や、製品の長期的な性能安定に大きく寄与します。この記事では、サブゼロ処理の定義や効果、工程、対象素材、他の熱処理との関係、導入時の注意点まで、専門的かつわかりやすく解説していきます。
サブゼロ処理とは何か?
サブゼロの意味と処理温度の範囲
サブゼロとは、「氷点下(0℃未満)」という意味を持つ言葉です。熱処理におけるサブゼロ処理とは、焼入れ後の鋼材を常温よりもさらに低温、一般的には−80℃から−196℃程度まで冷却する工程を指します。この処理を行うことで、常温では変態しきれずに残っていたオーステナイトを、マルテンサイトへと変化させることが可能になります。温度帯の違いにより効果やリスクが変わるため、目的や素材に応じた温度設定が重要です。
一般的な焼入れとの違い
焼入れは、加熱→急冷によってオーステナイトをマルテンサイトに変態させ、鋼を硬化させる工程ですが、常温付近では変態が完了しないことがあります。とくに冷却後に残る「残留オーステナイト」は、寸法変化や硬度低下の原因となります。サブゼロ処理では、この残留オーステナイトをさらに低温で強制的に変態させるため、焼入れ後の仕上げ処理としての役割を持っています。
どのような目的で行う処理なのか
主な目的は3つあります。第一に、残留オーステナイトの除去による硬度と寸法の安定化。第二に、経時変化による歪みや割れのリスク軽減。第三に、部品の耐摩耗性や疲労強度の向上です。これにより、長期間にわたって高い性能が求められる工具や金型などに対して、有効な手段となります。
サブゼロ処理が必要とされる理由
残留オーステナイトの影響とは
焼入れ後の鋼材には、完全にマルテンサイト化せずに残ったオーステナイトが存在することがあります。この残留オーステナイトは、外部応力や使用中の温度変化によって徐々に変態を起こし、体積変化を伴うため、寸法や形状の狂いを引き起こす要因になります。工具や精密部品では、この微小な変形が致命的な不良につながることもあります。
寸法安定性と精度維持の観点
サブゼロ処理により、焼入れ直後に残っている不安定なオーステナイトを処理することで、寸法変化のリスクを事前に取り除くことが可能になります。とくに再研磨が難しい金型や、厳しい公差が求められるシャフト・ピン類などでは、長期的な精度維持のためにこの処理が不可欠です。
工具や金型の長寿命化との関係
摩耗や衝撃を繰り返し受ける工具や金型では、内部の組織安定性が寿命に直結します。残留オーステナイトが多く残ったまま使用すると、摩耗が進みやすく、欠けやすくなる傾向があります。サブゼロ処理によって組織を均一かつ安定化させることで、耐久性の向上が期待できます。
サブゼロ処理のプロセスとタイミング
焼入れ後に処理する理由
サブゼロ処理は、焼入れ後すぐに実施するのが一般的です。これは、焼入れ直後の鋼材がまだ高温から急冷された状態にあり、組織変化が継続中であるため、このタイミングで処理を行うことで、より効果的に残留オーステナイトを変態させることができるからです。焼戻しよりも前に行うのが原則となります。
冷却方法と処理時間の考え方
冷却にはドライアイス(-78.5℃)や液体窒素(-196℃)を使用します。ドライアイスは比較的取り扱いが容易で安全性が高く、寸法安定を重視する用途に適しています。液体窒素は深冷処理とも呼ばれ、マルテンサイト変態の完了率をさらに高めたい場合に使われます。処理時間は通常30分〜数時間が目安ですが、材質や部品の大きさにより最適値は異なります。
焼戻しとの関係と組み合わせ方
サブゼロ処理を行った後は、再加熱して応力を除去する「焼戻し」が必要になります。冷却で生じた内部応力を緩和することで、割れや脆化を防ぎ、実用上の強靭性を確保します。サブゼロ処理と焼戻しは、セットで行うことで最大限の効果を発揮します。
サブゼロ処理の代表的な温度帯とその効果
ドライアイス冷却(約-80℃)
ドライアイスは手に入りやすく、汎用的な冷却手段として広く使用されています。冷却速度も比較的緩やかで、鋼材の割れリスクを抑えながら残留オーステナイトを効果的に変態させることができます。一般的な工具鋼や高速度鋼に対して、コストと安全性のバランスが取れた処理方法です。
液体窒素冷却(約-196℃)
液体窒素を使用する深冷処理は、より完全な残留オーステナイトの変態を促します。高精度な部品や、特殊用途で極めて高い硬度・寸法安定性が求められる場合に採用されます。ただし、冷却速度が速く、処理条件を誤ると割れやクラックのリスクが高まるため、精密な制御が必要です。
温度帯ごとの効果の違いと使い分け
ドライアイス冷却では安定性重視、液体窒素冷却では性能最大化が主眼となります。使用目的や製品特性に応じて、温度帯を使い分けることが重要です。どちらの方法を選ぶ場合も、処理前後の温度差や昇温・降温の管理が品質に大きく影響します。
処理に使用される設備と制御の工夫
専用のサブゼロ処理装置とは
サブゼロ処理には、専用の冷却装置が用いられます。これらは−80℃から−196℃の範囲まで温度を制御可能で、内部に処理対象のワークを収容し、一定時間冷却する構造になっています。装置内部は冷却ムラを防ぐため、気流制御や断熱構造が工夫されており、温度分布を均一に保つことができます。大量処理用の大型チャンバー式や、小型のボックス型装置など、処理対象や生産規模に応じた選択が可能です。
温度管理と昇温時の注意点
冷却時だけでなく、処理後の昇温(復温)過程も非常に重要です。急激な温度変化は熱応力を生じさせ、割れや変形の原因となるため、サブゼロ処理後はゆっくりと常温に戻す必要があります。温度の上げ下げは段階的に行い、所定のステップごとに保持時間を設けることで、材料内部に余計な応力を残さず、処理の効果を最大化できます。
自動制御とトレーサビリティへの対応
高品質が求められる製品では、処理温度・時間・昇温プロセスなどを自動制御できる装置が主流です。処理履歴をデータとして記録し、ロットごとにトレーサビリティを確保することが、品質保証の観点からも求められます。多品種少量生産の現場では、レシピ管理機能やバーコードによる追跡システムが有効です。
適用される素材と処理対象
高速度鋼やダイス鋼などの工具材
サブゼロ処理が最も効果を発揮するのは、高速度鋼(SKH)や冷間ダイス鋼(SKD11など)といった、硬度と靭性のバランスが求められる工具材料です。これらの材質は焼入れ後に残留オーステナイトを多く含む傾向があり、その変態処理としてサブゼロ処理が非常に有効です。耐摩耗性や耐欠損性の向上が期待できます。
焼入れ後の精密部品への適用
精密シャフト、スライド部品、転がり軸受など、寸法変化が許されない部品では、サブゼロ処理による安定化処理が有効です。とくに超精密加工を施した後では寸法補正が困難となるため、加工前にサブゼロ処理を入れておくことで後工程の品質安定につながります。
ステンレス鋼や合金鋼における効果
マルテンサイト系ステンレス鋼(例:SUS420)やニッケル合金鋼などでも、サブゼロ処理によって硬度向上や応力緩和効果が得られる場合があります。素材により処理効果の出方は異なるため、事前に熱処理メーカーと処理テストを行い、目的に合ったプロセスを設計することが推奨されます。
他の熱処理工程との違いと補完関係
焼入れ・焼戻しとの役割分担
焼入れは硬化処理、焼戻しは靭性付与、サブゼロ処理は寸法安定化と、それぞれの熱処理には異なる役割があります。サブゼロ処理は単独で完結するものではなく、焼入れと焼戻しの間に挟むことで、全体の処理効果を高める補完的な存在です。処理順を誤ると効果が半減するため、工程設計が重要になります。
サブゼロ処理の効果が発揮される範囲
サブゼロ処理はマルテンサイト変態を促進する処理であるため、オーステナイト系ステンレスやオーステナイト構造が安定な素材には適していません。焼入れでマルテンサイト化を狙う材質に限定して効果が出る処理であり、すべての金属に有効というわけではありません。
全体工程の中での位置づけ
サブゼロ処理は「高精度化」「高信頼性化」を実現するための追加処理として、工程全体の中で品質を底上げする役割を果たします。処理コストはかかりますが、寸法不良や寿命短縮による再加工・返品コストを防ぐといった観点から見れば、長期的にはコストメリットのある工程といえます。
処理導入時の注意点と管理項目
処理条件の設定ミスによるリスク
サブゼロ処理は適切な温度と時間を守らなければ、効果を得られないどころか、割れや構造劣化といったトラブルにつながる可能性があります。とくに急冷や過冷却による割れは、事前に十分な確認と試験が必要です。処理対象の材質や厚みを正確に把握したうえで、最適な処理条件を設計しなければなりません。
クラックや脆化の可能性と対策
急激な冷却によって内部応力が集中すると、マイクロクラックや遅れ破壊の原因となることがあります。これを防ぐには、冷却速度を制御できる装置の使用、昇温時の段階制御、焼戻しとの適切な組み合わせが不可欠です。とくに液体窒素による深冷処理では、割れに対する知識と経験が要求されます。
処理後検査の重要性
処理後は、硬度測定や寸法測定に加え、必要に応じて金属組織の観察なども行い、効果の確認と品質保証を行います。サブゼロ処理は外観からは分かりにくいため、処理証明書や工程データの記録も含めて、見える化とエビデンスが重要です。
よくある疑問とその考え方
なぜ常温以下まで冷やす必要があるのか?
焼入れ後、常温では変態が完了しない残留オーステナイトは、時間の経過や使用環境によって徐々に変態し、体積膨張を伴う変形を引き起こします。これを製造段階で確実に処理しておくために、サブゼロ温度まで冷却し、構造を安定化させることが求められるのです。
サブゼロ処理はすべての部品に必要か?
すべての部品に必須というわけではありません。処理が有効なのは、寸法精度が要求される製品や、繰り返し荷重・摩耗にさらされる高負荷部品などです。コストと効果のバランスを見極め、適切な場面で導入するのが基本となります。
外注する場合のチェックポイントとは?
外注先に依頼する場合は、サブゼロ処理の温度管理体制、処理後の品質確認方法、設備の対応温度帯、トレーサビリティの有無を確認しましょう。とくに深冷処理を希望する場合は、液体窒素を使った処理経験や安全管理の体制が整っているかを重視すべきです。
まとめ
サブゼロ処理は、焼入れ後に残る不安定な組織を安定化させるための重要な処理です。残留オーステナイトの除去、寸法の安定化、長期的な耐久性の確保など、多くのメリットがあります。処理温度や素材特性に応じたプロセス設計、工程間のタイミング管理、処理後の検査体制を整えることで、その効果を最大限に発揮できます。品質トラブルを未然に防ぎ、製品の信頼性を高めるためにも、サブゼロ処理の理解と活用は今後ますます重要になるでしょう。
会社案内資料ダウンロード
熱処理の詳細をもっと知りたい方へ!株式会社ウエストヒルの会社案内資料を今すぐダウンロードして、私たちのサービスと実績を確認してください。電気炉・装置・DIVA・SCRなどの熱処理設備や環境のご紹介、品質管理、施工実績など、あなたの課題解決をサポートする情報が満載です。