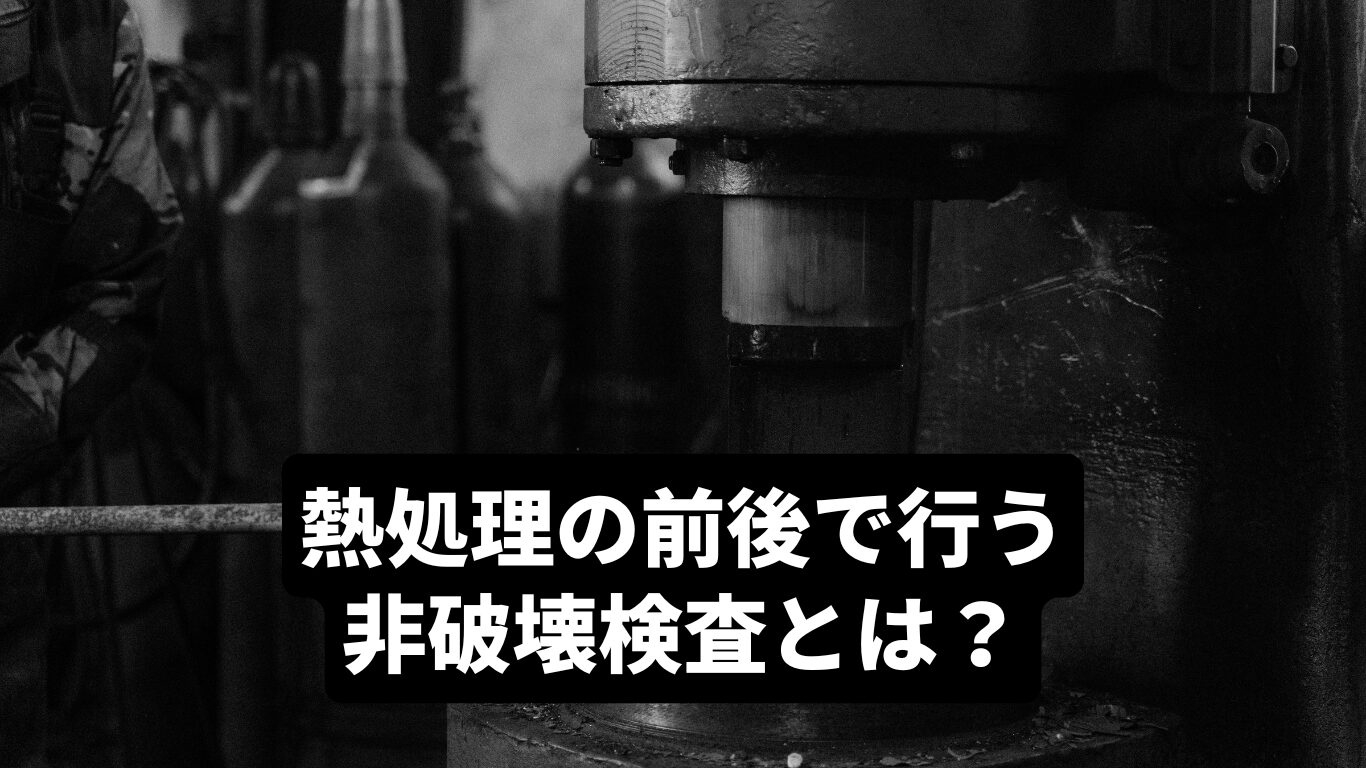
熱処理の専門知識をもっと深めたい方へ!今すぐ株式会社ウエストヒルの会社案内資料をダウンロードし、最新の技術情報と実績をご確認ください。
→ ウエストヒルの会社案内資料を無料ダウンロード
はじめに
熱処理は金属部品の強度や耐久性を向上させるために欠かせない工程ですが、その効果を確実に確認するには適切な検査が必要です。特に、内部欠陥や表面の異常を見逃すと、後の工程や使用時に重大なトラブルを引き起こす可能性があります。そのため、熱処理の前後に非破壊検査(NDT)を実施することが品質管理において重要な位置を占めています。本記事では、非破壊検査の概要から代表的な手法、熱処理との関係性、選定のポイントまで詳しく解説していきます。
非破壊検査とは何か
非破壊検査(Nondestructive Testing:NDT)とは、部材を破壊することなく内部や表面の欠陥を検出・評価する検査手法の総称です。対象物の機能や形状を損なうことなく検査できるため、製造工程だけでなく、保守や点検にも広く用いられています。非破壊検査は、欠陥の有無だけでなく、位置や大きさ、種類の把握も可能で、精密な品質管理や安全性評価に貢献します。
熱処理工程における非破壊検査の重要性
熱処理前後の非破壊検査は、以下の目的で実施されます。
- 加工前に材料内部の欠陥を検出し、熱処理に適した素材であることを確認する
- 熱処理後に発生する可能性のあるクラックや脱炭、組織変化などを評価する
- 製品としての品質保証とトレーサビリティを確保する
特に焼入れや浸炭処理のように温度差や組織変化が大きい工程では、表面および内部にストレスが蓄積されやすく、予期せぬ割れなどが発生するリスクがあります。そのため、適切な非破壊検査を組み合わせることが、製品の信頼性を高める上で不可欠です。
主な非破壊検査の種類
浸透探傷検査(PT)
表面の微細なクラックや欠陥を検出するための手法です。蛍光または着色された浸透液を塗布し、一定時間放置した後、表面を洗浄し、現像液を用いて欠陥からにじみ出た浸透液を可視化します。主に非磁性体や非鉄金属、焼入れ後のクラック検出に適しています。
磁粉探傷検査(MT)
磁性材料に対して使用される手法で、磁場を印加し、欠陥部に生じた磁束の漏れに磁粉が集まることで、欠陥位置を視覚的に把握します。鉄鋼製品の溶接部や焼入れ部品の表面割れの検出に効果があります。
超音波探傷検査(UT)
超音波を用いて内部欠陥を検出する方法です。探触子から発信された超音波が材料内部を伝播し、欠陥に当たって反射する信号を受信することで、欠陥の位置や大きさを特定します。比較的厚みのある部材や構造部品の検査に向いています。
放射線透過検査(RT)
X線やγ線などの放射線を照射し、内部を透過した線量をフィルムやセンサーで検出する手法です。内部の空洞や割れを画像として視覚的に確認できますが、安全管理や設備面での制約があります。
渦流探傷検査(ET)
導電性のある材料に交流磁場を与え、誘導される渦電流の変化を測定して欠陥を検出する方法です。表面および近傍の欠陥検出に優れ、航空機部品などの厳格な品質要求がある分野で活用されています。
熱処理工程ごとに適した非破壊検査
焼入れ・焼戻し工程
急冷によって発生するマルテンサイト変態による残留応力や、急激な温度変化による割れのリスクがあるため、磁粉探傷検査や超音波探傷検査が適しています。微細な表面割れの確認には浸透探傷検査も有効です。
浸炭・窒化処理工程
表面硬化処理の均一性や表面欠陥の有無を確認する目的で、浸透探傷検査や渦流探傷検査が使用されます。硬化層の深さについては切断検査などの破壊試験が用いられることもありますが、非破壊での深さ推定には先進的な渦流プローブを活用するケースもあります。
焼鈍・応力除去焼鈍工程
材料組織の変化による内部応力の残存状況や、新たに発生した内部欠陥の有無を評価する目的で、超音波探傷検査が有効です。高温による変形の影響が表面に及んでいないかを確認するために、補助的に浸透探傷検査を併用することもあります。
検査方法の選定基準
非破壊検査を選定する際には、以下のポイントを考慮する必要があります。
- 材質:磁性の有無や導電性によって適用可能な検査が異なる
- 欠陥の種類:表面欠陥か内部欠陥かによって検査手法を分ける
- 部品の形状:検査装置が対応可能な寸法や形状であるかを確認
- 作業環境:安全性や検査スピード、現場での実施可否
- コストと精度のバランス:必要な精度に見合ったコストであるか
これらを踏まえ、目的に応じて最適な検査手法を組み合わせることで、効率的な品質保証体制を構築できます。
非破壊検査を導入するメリット
非破壊検査の導入により、製品品質の安定化、歩留まりの向上、顧客信頼の確保といった効果が期待できます。目視や破壊試験では見逃しやすい微細な欠陥を高精度で検出することで、トラブルの未然防止が可能となり、製品クレームやリコールのリスクも低減されます。加えて、加工後の再修理や廃棄を減らすことができるため、製造コストの削減にも寄与します。
検査結果の活用と品質保証への応用
非破壊検査で得られたデータは、単なる合否判定にとどまらず、製造工程の改善やトレーサビリティの強化にも活用できます。検査履歴を記録・管理することで、後工程や出荷後の品質保証にもつながり、顧客に対して信頼性の高い製品を提供する基盤となります。AIやデジタル技術と連携することで、検査データの自動分析や予兆検知も実現可能となり、より高度な品質管理体制へと進化できます。
まとめ
熱処理工程における非破壊検査は、品質保証の要として欠かせない存在です。適切な検査手法を選定し、工程の前後で効果的に活用することで、製品の信頼性と安全性を高めることができます。導入の際には、目的・部品特性・作業環境に応じて最適な方法を検討することが重要です。この記事を参考に、自社製品の品質向上に向けた非破壊検査の活用をぜひご検討ください。
会社案内資料ダウンロード
熱処理の詳細をもっと知りたい方へ!株式会社ウエストヒルの会社案内資料を今すぐダウンロードして、私たちのサービスと実績を確認してください。電気炉・装置・DIVA・SCRなどの熱処理設備や環境のご紹介、品質管理、施工実績など、あなたの課題解決をサポートする情報が満載です。